Uncover the real root causes of inventory accuracy issues
Sometimes, managing inventory can feel like keeping a row of dominos standing – one issue can bring everything tumbling down.
To solve these issues and maximize inventory accuracy, you have to consider your entire supply chain and look beyond the symptoms. When you can identify the reason behind a symptom, ask, “why is this reason happening?” Continue this question-and-answer process until you reach the fundamental – or root – cause. This process is called Root Cause Analysis, and it is a powerful tool for solving inventory issues.
In our experience, the overwhelming majority of root causes fit into five categories. Understand these real root causes and you’re well on your way to solving any inventory accuracy issue:
1. Lack of appropriate technology
Think about how many apps you have downloaded on your phone and how few you use on a regular basis. Why? Most apps are not easy to use (some make the user’s life harder). The same goes for technology solutions in the workplace. What stock officer wants to slow down business and frustrate their colleagues to document returns in a cumbersome application? Technology has to work for your business, not the other way around.
2. Lack of processes and procedures
If you need certain things to be done right every time, you have to have defined and documented processes. Without processes and procedures, people will handle things in an ad hoc manner with little to no consistency. On top of that, there is also a perceived lack of importance, as well as a lack of management support, when processes are not clearly defined and documented.
3. Inadequate user training
As supply chains expand around the world and become increasingly complex, new skills are required for task execution and decision making. Training on processes and procedures is critical to maintaining inventory accuracy. Be sensitive to each user’s unique background and experience. Training should be conducted to bring diverse groups of people to a consistent level of job performance.
4. Poor warehouse design
You need to know where everything is in your warehouse—down to the sector, aisle, shelf, and shelf placement. Randomly putting items in places for convenience causes inventory nightmares down the road. Document your warehouse and clearly mark everything, down to the shelf. Ensure that you have good lighting, adequate storage space, and enough room to move.
5. Not having the right people in the right place
Internally, people with experience and vision should be encouraged to assume leadership roles. People who are intimidated at the thought of using a computer should not be expected to pioneer a new inventory management system. Externally, look at your suppliers, consultants, and partners. Do they share your passion about inventory management? Can they support your organization, or would they just hinder your progress? Having the right people in the right places makes it easier to address all the other root causes and may prevent some issues from ever taking place.
Example: Root Cause Analysis with a Fishbone Diagram
Let’s walk through an example of how Root Cause Analysis can be used to solve a real issue with inventory accuracy. We will be using a tool known as a fish bone diagram to help visualize the many cause-and-effect relationships at play. On a fish bone diagram, each arrow represents a cause that feeds into an effect. Sometimes, that effect is also the cause of another problem further down the chain. Eventually, all of the causes feed into the main issue that we are concerned about.
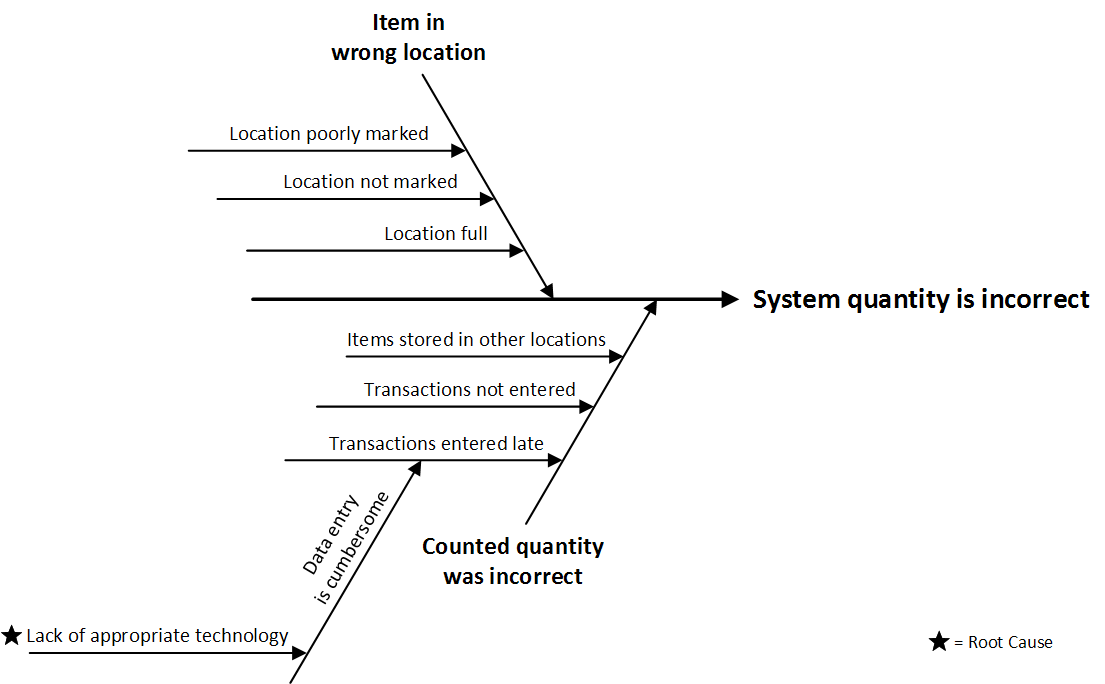
In our example scenario, someone has noticed that an item’s quantity in our inventory system is incorrect – the system shows 10 units in inventory, but when they check the shelf, there are only two units left. In brainstorming possible causes for the discrepancy, they consider two possibilities: (1) the remaining eight units are around somewhere, they have just been placed into the wrong location, and (2) the system quantity has gotten off track and is now incorrect. Investigation reveals that the items are nowhere to be found, and attention is turned to the second possibility.
There are several reasons why the system quantity may get off track, but a very common one is that users do not enter their transactions into the system (or they enter them late). In our example, it turns out that some users were writing transactions down on paper and waiting to perform data entry until the end of their shift. Sometimes it took several days to get all of the transactions entered into the system, and in the meantime the system quantities were incorrect. When asked about their practice, these users said that data entry in the current system is so cumbersome that they had to wait until the end of the day so that they didn’t interfere with their colleagues’ work. The last step in our investigation is to find the cause of this difficulty for our users. This brings us to the first root cause identified in the section above, Lack of appropriate technology. In our case, the inventory application doesn’t allow users to easily enter data while they work. We can now work on finding a solution to this root cause, and our inventory accuracy will improve because of it.
In our next blog, we’ll dive into more detail on selecting the appropriate technology for use in your warehouse to achieve greater accuracy and efficiency.